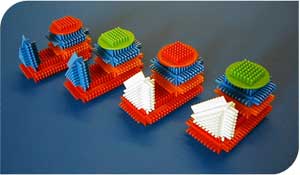 |
The training session begins with a production line set up to
build the four products (shown here) using traditional batch production
methods. There are four assembly stages, which can be associated with
similar, real life processes, a component stores and at least one supplier.
During the production run the customer places a series of orders for
the product, which causes more demand for kits of parts for the
|
production line. At the end of the timed session the production line
is halted and the process is evaluated and performance critically measured.
This includes counting the value of products manufactured, the cost
of any defective products found at final inspection, the cost of raw
materials on the production line and the cost of part-built products
(work in progress).
|

The trainees are then invited to discuss the results and to suggest suitable
ways of improving production techniques and reducing costs. Two of these suggestions
are then implemented and the game is run again to assess the impact of the
changes. The process of making changes, testing and evaluation is repeated,
usually four times, reducing until a more effective production line has been
created.
The key
areas for the improvement of business performance are typically:-
-
Production Line Layout Improving the flow
of materials with lineside supply and the flow of sub assemblies through
the process to a One Piece Flow.
-
Fool-proofed Quality Presenting the raw
materials in such a manner as to reduce the possibility of incorrect orientation
during assembly. Also development of better assembly instructions and
quality checking.
-
Cellular Manufacturing Changing the production
method from batch oriented to cellular flow manufacturing reducing the
amount of stock on the production line and checking quality at all stages
of manufacture
The game
is supplied fully boxed with comprehensive instruction manuals.